Why choose ForrestBrown?
When it comes to R&D tax credit claims, ForrestBrown is the premier provider in the UK. We were named ‘best independent consultancy firm’ at the Taxation Awards 2023 in recognition of our technical excellence and service innovation. We bring together a specialist team that gives you access to unrivalled technical firepower. We use a rigorous, continually-improving process to deliver a claim that stands up to HMRC scrutiny.
To find out more about claiming R&D tax credits with ForrestBrown, contact our expert team today:
- Telephone
- 0117 926 9022
- hello@forrestbrown.co.uk
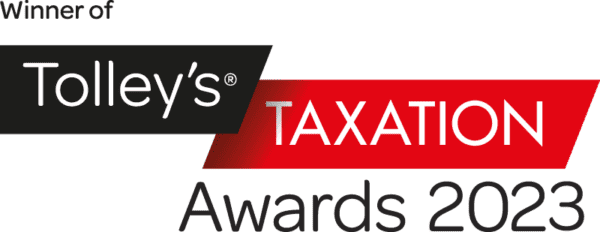
Winner
Best Independent Consultancy Firm
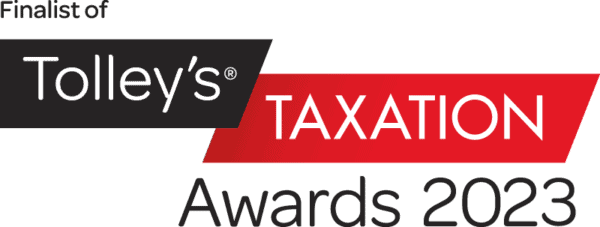
Finalist
Best Employer in Tax
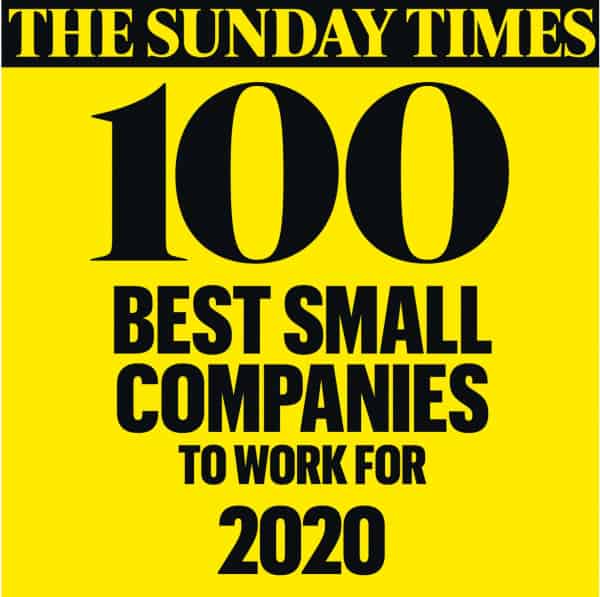
#73 out of 100
The Sunday Times Best Companies to Work For
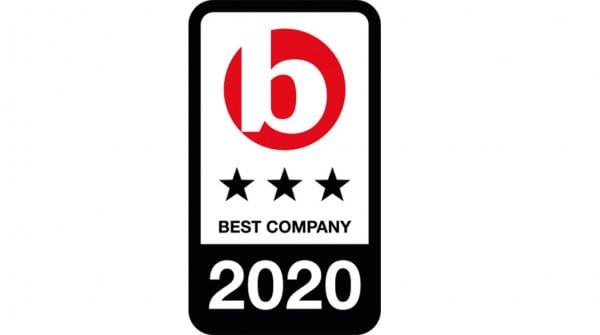
3 star accredited
Best companies – “extraordinary” levels of employee engagement
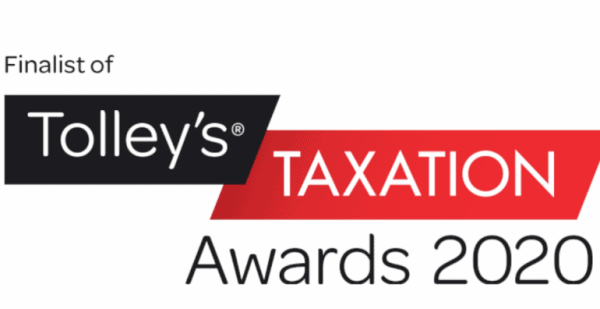
Finalist
Best Employer in Tax
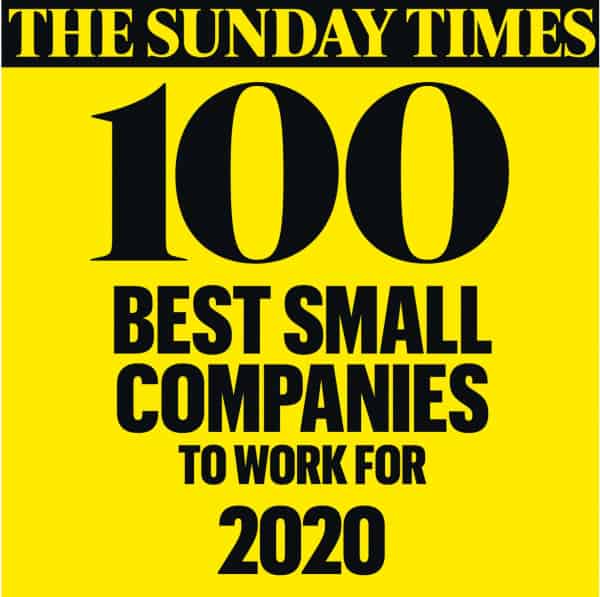
#73 out of 100
The Sunday Times Best Companies to Work For
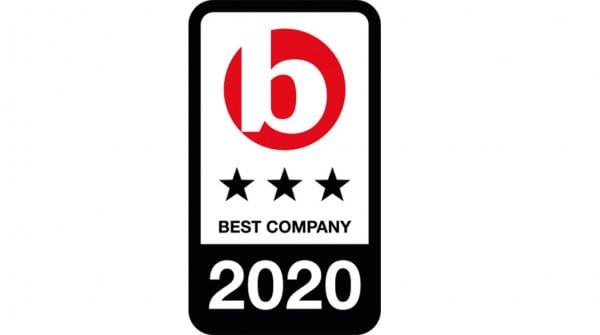
3 star accredited
Best companies – “extraordinary” levels of employee engagement
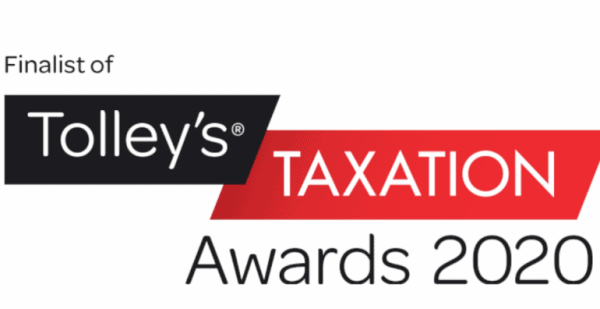
Finalist
Best Employer in Tax