Developing new pharmaceutical drugs is one of the biggest areas of research and development (R&D) globally, with large amounts of money invested. In 2021 over $238 billion was invested in R&D in the pharmaceutical sector worldwide. It is therefore an area where grants and R&D tax relief claims are widely made . Some companies involved in and around the pharmaceuticals supply chain are carrying out qualifying R&D projects but are not claiming R&D tax relief or Patent Box relief. This means they could be missing out on relief or cash to spend on further R&D.
Research and Development in the Pharmaceutical Industry
Most companies are comfortable knowing that the development of new drugs is likely to be R&D, however, fewer companies know that developing or adapting a manufacturing process for a new drug could be eligible for R&D tax relief. In addition, activities like developing new testing techniques and methodologies could allow a company to claim even if they’ve had nothing to do with the drug development itself. This means that manufacturers who develop innovative, cost-effective ways to produce products, suppliers of equipment and specialist testing companies could also qualify for R&D tax relief.
Qualifying R&D costs in pharmaceutical industry occur when a project seeks to achieve an advance in science or technology through the resolution of scientific or technological uncertainty.
The definition applies equally to products, processes, materials, devices and services. It also applies to new inventions or appreciable improvements to existing things. It is important to remember that your advance needs to be in science or technology and that you need to be pushing the boundaries of the scientific or technological baseline in your field.
Types of R&D in the pharmaceutical industry
Nowadays the development of a pharmaceutical product is much more collaborative and involves other parties, such as packaging designers and manufacturers. The lifecycle of a drug begins at drug development and ends with the production of a cost-effective commercialised product. R&D takes place along that entire supply chain.
What qualifies as R&D in pharmaceuticals?
Due to market demands, drugs need to make their way to patients faster and cheaper whilst still meeting regulatory requirements. There is a need in the pharmaceutical industry to speed up the process of bringing new drugs to market and cutting the costs involved. Amazing drugs are being held up. This need for speed has an impact on businesses that look to improve processes in order to achieve this.
Developing/adapting a pharmaceutical manufacturing process for a new drug
As with any manufacturing process, there are numerous targets to measure in pharmaceutical manufacturing. These will include wastage, cost effectiveness and quality amongst others. Being a highly regulated industry, product quality and regulatory compliance in pharmaceuticals is essential.
Adapting a manufacturing process could create a faster line through automation, improving the technology used in that process or speeding up ingredient measurement for example.
With pharmaceuticals manufacturing, you can’t simply increase production. Chemicals can interact and behave differently when produced at different rates, volumes, or in certain environments. Developing a new machine that can handle 1000 more tablets a minute will need to be rigorously tested to ensure the chemical formulation remains intact and the same end product is guaranteed.
Improving drug delivery systems
There are a number of small and medium-sized enterprises that don’t develop new drugs (this takes several years and significant funds) but look instead at improving the delivery of old drugs for quicker returns. These can be intense projects when it comes to R&D.
The focus can be on improving the efficacy of drugs, creating new formulations and delivery methods. These companies add value by making it easier and more convenient to take or use the drugs as well as lowering manufacturing costs. At the same time, they look to advance patient safety, reduce drug toxicity and maintain product stability.
The development of alternative and new drug delivery routes and overcoming delivery challenges requires the use of innovative approaches and is often qualifying R&D expenditure.
Some companies focus on creating variations on existing drugs where deployment is improved. This can be looking at less invasive delivery methods such as developing needle-free technologies like a topical delivery system for the flu vaccine or insulin delivery in diabetes patients.
Developing alternative delivery methods also allows pharmaceutical companies to differentiate their product in a crowded market and reposition existing drugs.
The other key area looks at more targeted drug delivery, focusing on a particular tissue or even group of cells. For example, in cancer treatment the targeting of drugs is on a cellular level, the aim being that cancer cells are targeted without impacting other cells.
Each therapeutic area also has its own unique set of delivery needs. There are pharmaceutical companies that are looking at ways to improve aspects of delivery to benefit the patient. For example, in oncology, drug delivery companies are finding new ways to deliver existing molecules.
Creating personalised medicine
In an increasingly patient-centric world, the experience of the end-user is more important than ever. This has seen a surge in R&D where a drug or device has been developed specifically to better meet the needs of a user. If a user has a better experience, they will have more confidence in the drug and are more likely to continue to use the product.
As the experience of patients is becoming more of a priority, there has been a move towards increasingly personalised medicine. Personalised medicine looks at ways to combine products to better meet individual needs and improve their quality of life. For example, some companies are using technology to extend the release of certain drugs, particularly useful for those patients managing chronic pain.
Using AI in Pharma R&D
In recent times, AI has become a viable tool for drug discovery, as well as offering insight into potential drugs that could be repurposed or improved. For example, Bayar currently uses AI alongside researchers at Imperial College. By reducing the cost of the early stages of drug production, pharmaceutical companies can choose the most desirable drug to take to clinical trials. As clinical trials tend to be one of the most costly stages of drug development, this allows companies to focus more on drug candidates more likely to return higher value.
Improving Storage Solutions for Pharmaceuticals
Stockpiling pharmaceuticals is potentially difficult with many drugs, such as vaccines, requiring refrigeration to maintain efficacy. Stockpiling pharmaceuticals remains vitally important, however, allowing for efficient deployment in times of high demand.
Stable Pharma worked closely with ForrestBrown to claim R&D tax relief for their innovation, when developing StablevaX. StablevaX is a technology that produces fridge-free vaccines, in order to reduce wastage and save lives.
By being rewarded for their work on StablevaX, Stable Pharma invested in further R&D, showing just how vital R&D tax relief can be for pharmaceutical companies. R&D tax relief is also powerful in allowing larger companies to allocate resources to a variety of different R&D ventures.
Making pills easier to swallow
With the focus on the user, drugs need to be easy to take and be as pleasant an experience as possible. It is also necessary for drugs to look different to others so that they can be easily distinguished.
Companies are therefore looking at reducing the size of pills and adapting the shape to meet needs. This is key for children.
Taste has a huge impact on the user experience around a drug and a person’s ongoing use of it. Many drugs are bitter tasting. In children, this is a particular obstacle.
There is R&D in utilising and developing taste-masking technologies such as polymer coatings to stop the drug coming in contact with taste-buds and using masking agents like flavourings and sweeteners.
Hermes Pharma is the first company to develop hot melt coating (HMC) to successfully mask the sour and metallic taste of pharmaceutical ingredients. HMC technology is widely used in the food industry to prevent ready meals absorbing too much water and was adapted by Hermes Pharma to mask the bitter taste of acetylcysteine.
Combinations and collaborations in the pharmaceutical industry
In the pharmaceutical industry, we are seeing more collaboration between small and medium enterprises (SMEs) and larger manufacturers. This is often because larger pharmaceuticals are focussing their efforts on developing new drugs. The R&D focus for SMEs is often much narrower and more agile. They can then offer these services to larger companies.
One example is British group, Abzena, who provide a wide range of complementary technologies to research-based companies. They specialise in optimising the development of therapeutic proteins, antibodies and antibody-drug conjugates.
Pharmaceutical manufacturing and testing
The manufacture and testing of pharmaceutical products is highly regulated to guarantee patient safety. Thorough testing and analysis is required before any drugs get to market. The tests often generate data to ensure regulatory compliance in different markets.
Numerous companies carry out customised testing for the medical and pharmaceutical industries, producing studies of drugs and devices at various stages of production. Tests can be of raw and active pharmaceutical ingredients, the materials that make up the vehicle as well as the finished products themselves.
Butterworth Labs are involved in the development of testing methods, with a focus on analysing the stability of products in storage.
New testing techniques and methodologies
There are a number of tests that drugs have to go through in order to be ready to go out to market. Typically, these standard tests are not applicable for R&D tax claims.
However, as soon as a company looks to develop new testing techniques or improve the process by using technology (automation / computing) to make the testing quicker, it potentially becomes a qualifying activity. Developing new testing techniques and methodologies could allow a company to claim even if they’ve had nothing to do with the drug development itself.
Improving drug testing process
If you are a pharmaceutical testing company, you may be looking at how technology can be used to speed up and cut costs around your testing process. This may be about automation or developing new technology.
Wickham Micro in Gosport specialise in microbiology and toxicology testing for the pharmaceutical industry. They are actively involved in the development of new testing methodologies, working closely with academics and pharmaceutical companies.
Claims testing drugs
In the marketing of drugs, in particular new versions of drugs, pharmaceutical companies want to be able to make claims about their product. Before companies can make these claims, they have to be tested scientifically. The most compelling claims tend to be around the efficiency and impact of the drug on the condition.
If you are a company that is involved in developing new methodologies to substantiate claims then this can be qualifying activity for R&D tax relief. These methodologies will be around the chemical analysis of the drug.
Challenges in testing pharmaceuticals
There can be unique challenges in testing products such as aerosols and inhalation devices as well as those pharmaceutical products that are difficult to handle, such as antibiotics.
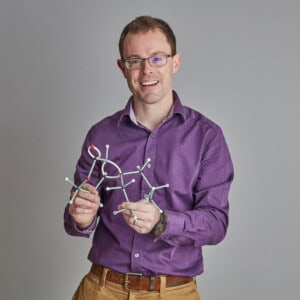
- hello@forrestbrown.co.uk
- Phone
- 0117 926 9022
- Highly experienced materials scientist.
- Background in food science, pharma and defence.
- Doctorate in organic chemistry.
Pharmaceutical Packaging development
When developing packaging for pharmaceuticals and the healthcare industry there are a number of key considerations. Primarily, you need to ensure that the items are kept as they should be. This is both a security issue and about preserving shelf life. They should also be environmentally friendly, made from sustainable materials where possible.
Pharmaceutical Product Design
Product design and packaging is also becoming more focused on the users. There are numerous ground-breaking and innovative projects looking to deliver for users when it comes to performance and ease of use.
If a company develops a new shape and size of drug, then there can be challenges around designing and manufacturing new compliant packaging. There are a number of companies in the UK developing innovative packaging solutions for pharmaceuticals. They are using and developing 3D printing, vacuum forming and CNC (Computer Numerical Control) technologies and techniques to aid in packaging innovation. These can include bespoke designs such as those created by Riverside Medical who make use of the ShawPak – a machine offering a thermoforming solution that helps them meet unique packaging needs.
The development of packaging in pharmaceuticals is a big area of R&D. Read more about R&D in plastics.
Challenges around pharmaceutical packaging
There are a number of challenges around packaging that cover the following:
- Combating counterfeit drugs
- Unit-dose control
- Child-resistant packaging
- Eco-friendly and sustainable packaging
Sustainable pharmaceutical packaging
One of the biggest challenges in pharmaceutical packaging is to use more sustainable materials. Tin foil and certain types of plastics used widely in packaging are not environmentally friendly so companies are looking at using alternative materials. These can include the use of biodegradable resources.
The challenge is to ensure that these materials are safe and fully compliant as well as cost-effective. These projects often involve research and development and should qualify for R&D tax relief.
There are a number of ways that people are looking to have less impact on the environment:
- Using sustainable materials
- Using recyclable materials
- Developing reusable packaging
- Reducing the amount of material used
- Reducing waste from damage and contamination
An example of innovation in sustainable packaging is DuPont™ Tyvek®. DuPont™ has developed a form of flashspun high-density polyethylene fibres for use in packaging that can be recycled or incinerated without leaving residue. It can even be used as fuel. The packaging designs also weigh less, require less space and are stronger.
Materials
As companies look to reduce costs, improve sustainability and speed up the manufacturing of packaging, they have to do so while meeting strict regulatory demands.
When using different materials and bringing them together in packaging, one of the biggest challenges can be getting them to bond together in the right way. Bonding plastic onto other types of plastic is particularly difficult and requires significant experimentation. This can be and is one area of qualifying R&D expenditure in pharmaceutical packaging.
Packaging and tackling drug counterfeit medicine
Patient safety is paramount for pharmaceutical packaging manufacturers. Therefore security and anti-counterfeiting is a priority, ensuring that patients get the drugs they need. There is a global campaign to fight against fake medicines.
Packaging now must consider tamper-evident features and anti-counterfeiting measures such as secure holograms and black-light verification. Companies even offer bespoke authentication systems and designs to meet unique briefs. Anti-counterfeiting technologies focus on seals and stickers. They need to be easy to apply but impossible to modify.
Ar Packaging (formerly Firstan), based in Cambridge, have invested in ‘in-line’ application of Sensomatic, checkpoint and various other security tags to ensure products are tamper-proof. Their ‘M-lock’ system gives a clear indication that any tampering has occurred.
Temperature-sensitive pharmaceuticals
It is essential that temperature-sensitive pharmaceuticals are kept at a consistent temperature, especially during transportation. This has seen a focus on temperature-controlled packaging (TCP) that enables a consistent temperature to be maintained and prevents the drugs from losing their efficacy.
Innovation in temperature-controlled packaging has involved a move away from water based-coolants to emerging technologies such as advanced phase-change materials (PCM) and vacuum insulated panels (VIPs). Some packaging even has ‘hibernation’ capabilities, allowing the drugs to be placed in a refrigerated area and remain protected for extended periods of time.
R&D tax relief and grant funding for pharmaceuticals
The interaction between R&D tax credits and grant funding is complex but also one that is important to investigate within pharmaceuticals.
The pharmaceutical sector is a popular recipient of grant funding. For the purposes of R&D tax relief for SMEs, it is critical to distinguish notified State Aid grant funding from other types of grant. If a project receives a notified State Aid grant, no matter how small, it cannot then benefit from an R&D claim under the SME scheme. For other types of grants and subsidies, a company can claim SME relief for non-subsidised costs. Under the large company R&D tax relief scheme (RDEC), there is no such restriction on grant funding, so expenditure which is excluded from an SME claim may be eligible for a large company claim (albeit at a lower level of generosity).
This means that you will need to carefully consider and weigh up the benefits of each grant for each project in relation to the cash boost offered by an R&D tax credit. Read more on the interaction between grants and R&D tax incentives
Patent Box tax relief for pharmaceutical companies
The Patent Box regime rewards pharmaceutical innovators for keeping their intellectual property (IP) within the UK by reducing any corporation tax on profits from any qualified IP income to 10%.
With corporation tax having increased from 19% to 25% on April 1st 2023, there’s even more reason for companies in the pharmaceutical industry to take the time to make the most of patent box tax relief.
Can the pharmaceutical industry benefit from Patent Box tax relief?
Many pharmaceutical companies may not realise that their IP is patentable, and will be missing out on valuable tax relief. In fact, most patented inventions are simply minor technical improvements on a product or process that is already out there.
Companies in the pharmaceutical industry choosing to innovate by improving existing drugs and processes are prime candidates for utilising patent box.
If you have developed an innovative product or process in the pharmaceutical industry, there may be an opportunity to reduce your corporation tax for any profits generated from your patented invention, allowing you to have more funding available for R&D in the future. At ForrestBrown, our team of chartered tax advisers understand the complexities and can advise on R&D tax relief and UK Patent Box relief. We are more than happy to discuss your project and use our expert knowledge to help you make the most of your innovation.
R&D and consumables rule changes
The changes to the rules around R&D and consumables (introduced in April 2015) restrict R&D relief where materials costs are used for R&D purposes, but are also part of an end product sold to a customer.
Before the rule changes, there was no formal exclusion for these costs, although large claims were subject to intense scrutiny by HMRC. The rule means that any costs relating to materials or components, which form part of an item sold in the ordinary course of business won’t be eligible for R&D relief. In order to ensure that you are submit a robust claim, it is essential for companies to keep clear records to show exactly what was used in the manufacturing or R&D process.
Jenny Tragner, one of our directors, explains in more detail the changes to consumables in R&D claims.
Overseas R&D – Rule Changes
Another potential rule change in 2024 will see restrictions on UK companies carrying out their research and development abroad.
The idea is that this will encourage UK companies to work with more local businesses, although it may reduce the amount of international collaboration for pharmaceutical companies.
ForrestBrown – experts in pharma R&D tax relief
Innovative pharmaceutical companies throughout the supply chain could be missing out on R&D tax relief. This is because they don’t know it exists or are confused by the definition of R&D and don’t believe it applies to their business activity.
The misconceptions don’t end there and we often find businesses are confused about what activities qualify. For example, work undertaken on behalf of a client can be included in some instances. Getting your R&D claim right is important so it’s important to partner with a specialist.
At ForrestBrown, we take the time to understand how the definition of R&D applies to your business and help you identify and log R&D projects and activities.
For large companies, we can also implement an appropriate record keeping system to improve the methodology of your future claims. To find out more contact our pharmaceutical R&D claim advisers, on 0117 926 9022 or email ForrestBrown at hello@forrestbrown.co.uk