This is the unabridged version of a ForrestBrown industry thought-leadership article from our senior sector specialist Pete Beavis MSci PhD that was first published in European Plastic Product Manufacturer.
While much of the public may disagree, I firmly believe plastics and the polymers that comprise them are wonder materials. Without them, we would be lost. They touch nearly every part of our lives, from medicines and manufacturing to finance and food. They have many far-reaching benefits.
At the time of writing, during the COVID-19 pandemic, our front-line NHS staff depend on plastic in personal protective equipment and patients rely on plastic to deliver the medicines they need. In these times of social distancing, the importance of reliable and sustainable food supply chains has never been more evident – and in which the appropriate use of plastics is crucial.
It’s also easy to forget that the UK wastes 9.5 million tonnes of food each year. This would be significantly higher without packaging that keeps produce protected and fresh for longer. If we removed plastic from the equation, the resources, energy and transport required to grow and deliver a significant proportion of our food would all go to waste.
But with this belief comes a colossal burden. It’s no secret that plastic is also an immense problem. The WWF calculates that total plastic waste generation will be around 6.3 million tonnes by 2030. Herein lies the problem. It’s not plastic per se, but the amount and way we use it combined with the impact it has on the natural world after it’s served its initial purpose.
Sustainable packaging
Which is why we often hear about so-called ‘bioplastics’ that are going to save the world – ‘bio’ is synonymous with ‘clean’ and ‘green’. Be they bio-based equivalents derived from renewable resources, or comprised of biodegradable polymers, they’re hailed as the new materials that will end our reliance on conventional fossil-fuel derived plastics. They get headlines in the same way new “cures for cancer” are regularly written about in the tabloids.
Yet it’s always more complicated than this and there is no silver bullet for all materials and every application – bio-based materials strive for carbon neutrality but not necessarily biodegradability. Biodegradable materials’ structure and associated additives may mean that promises are not lived up to in a real-world waste stream and with less-than-optimum environmental conditions. Irrespective of any genuine green(er) credentials, they don’t lessen the impact that poorly-disposed waste has on the environment and they don’t go any way towards lessening the impact of the production process through reducing demand.
Packaging recycling
Recycling as a bastion of green policy is problematic too – polymers degrade with every step of (re)processing and recycling, meaning that the material is inherently life-limited, and achieving fully-recycled content in a functioning product is generally unfeasible. Clearly we mustn’t pin all our hopes on any single class of materials or one trait above all others.
The huge variety of man-made and modified materials is the epitome of innovation – be they in the materials themselves, the manufacturing processes, or the waste stream. And this innovation is continuing even if the advances are too subtle or self-evident to be headline-grabbing.
I believe it’s far more attractive to promote an approach of continual innovation in the production and use of plastics, whereby each improvement may individually be small. But by tackling the issue bit by bit, we can find ways to make plastic far less damaging, while still benefitting from its properties.
In essence, we need to use less of it, make it more recyclable and ensure it doesn’t cause havoc in the oceans. Sounds simple, doesn’t it? Perhaps not, but there are plenty of unsung heroes innovating every single day towards achieving this. They’re quietly working away without the thanks they deserve. In fact, quite the opposite. Despite trying to make a difference – and working towards the same goal as many environmentalists – they’re often vilified for being involved with a material that can be so troublesome, but which we all desperately need.
Plastic’s image problem is not inherent to the material. After all, it becomes pollution only when it becomes discarded plastic. The very embodiment of pollution is actually mankind’s actions and their damaging impact on the environment.
Heroes of packaging design, processing and materials handling
All this begs the question, who are these unsung plastic heroes and what are they doing? A great example is a firm called Kinnear Dufort Designs. Its team has created the Abbey Well twistable bottle. It may be a single use plastic, but it’s 100 per cent recyclable and has been designed to be easily twisted into a much smaller shape when empty, thus saving a huge amount of space in the waste management process. Not only that, it uses 32 per cent less plastic than the previous bottle designs, and is a key step to engaging with consumers on sustainability, or at least reducing the product’s impact.
Packaging design
Another is Aegg, which found a way to replace polystyrene sheet containers with polyethylene terephthalate (PET). The former of the materials has great functionality but is not widely recycled primarily because the waste stream is not widely accessible or commercially attractive. PET, on the other hand, is widely recyclable. The challenge was to find a way to process PET via injection moulding for the job in hand in place of the conventional blow-moulding technology. The team overcame that hurdle and has therefore made a small but important step towards a more readily recyclable product, albeit one still manufactured from synthetic polymers.
Packaging manufacturing
Meanwhile, I recall MuCell found a way to cut the use of plastic in chocolate bar wrappers. As a nation, we eat nearly 509 million kilograms of chocolate a year. That equates to a lot of packaging. The firm innovated to create a three-layer wrap with a foamed core. This was just 100 micrometres thick overall with the ‘micro-foamed’ middle layer 50 micrometres thick. The strength isn’t affected, but it uses 15-20% less plastic. With millions of bars flying off the shelves every year, this makes a significant difference in the amount of materials consumed and also in the energy to transport the product to the supermarkets and the end consumer.
Taken separately, none of these innovations solve or even come close to addressing all of our concerns and hopes for plastics and packaging. However, whilst unlikely to grab the front-page headlines, they do represent advances in their respective scientific and technological fields. Each will contribute to significant improvements in materials, their impact on resources, and consumer behaviour. All are worthy of recognition, certainly within their disciplines/sectors, as genuine advances.
If you add up all these little incremental innovations across all industries and countries, it makes a huge impact. Many small changes combined add up to a revolution. Moreover, if we continue in this direction, we’ll eventually turn a corner when it comes to the plastic problem.
Innovation in the packaging supply chain
Contrary to their depiction in the mass media as resource-hungry, waste-generating perpetuators of throw-away culture, the polymer and plastics industry is very keen on becoming more efficient and less damaging. Not only does it cut costs, but consumers are demanding it and more importantly, it’s the right thing to do.
The Government is also doing its bit to drive change. A plastic packaging tax will come into force from April 2022. Furthermore, manufacturers and importers whose products have less than 30 per cent recyclable material will be charged £200 per tonne according to the recent budget announcement from the Chancellor.
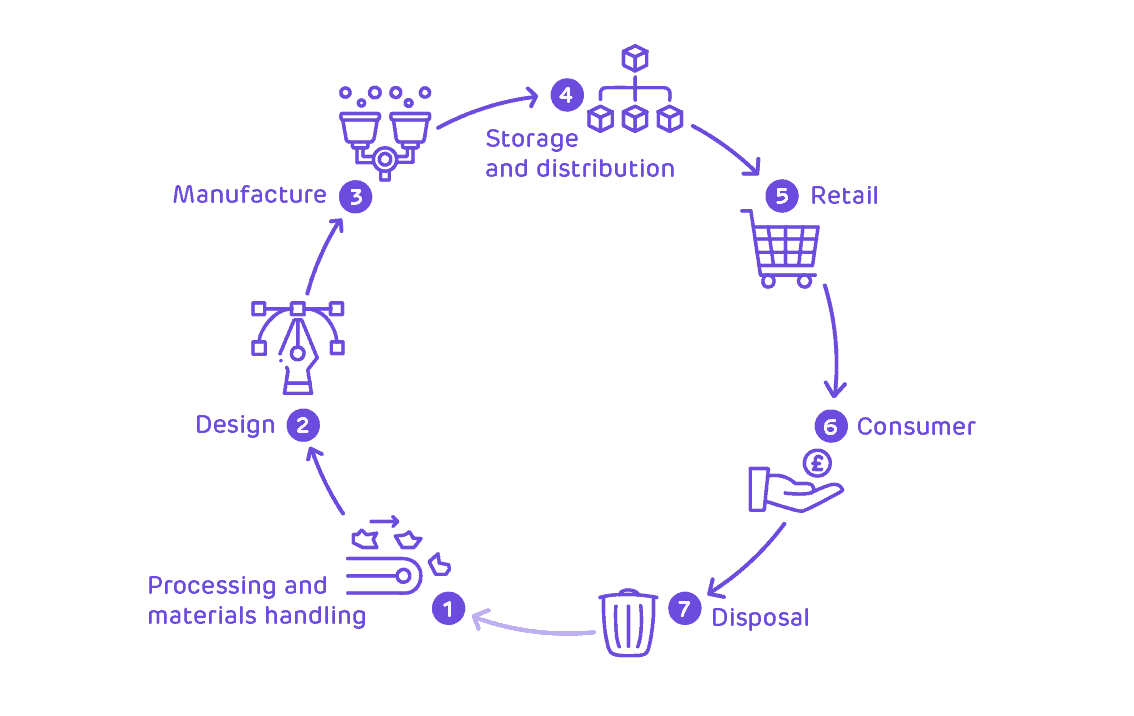
Packaging R&D – supporting innovation with R&D tax credits
However, it doesn’t stop there. All this innovation is supported through research and development (R&D) tax credits, meaning every development – large and small – is incentivised. The credits are a valuable source of cash for businesses to invest in accelerating their R&D, hiring new staff and ultimately growing.
They’re open to any business that spends money developing new materials, products, processes or services; or enhancing existing ones. The claim results in either a cash payment, a Corporation Tax reduction, or both. The scope for identifying R&D is huge – in fact, it exists in every single sector. And if you’re making a claim for the first time, you can typically claim R&D tax relief for your last two completed accounting periods, then every one going forward.
Such funding is vital because we need to attract the brightest and best to a sector where they can make a real difference and contribute to solving some of our planet’s current issues, where they can both be proud to be able to make a difference and receive the recognition they deserve. This is the true path to reducing the plastic we use, making better and longer lasting plastic products, and ensuring what’s created is recyclable and doesn’t end up in our seas.
In these challenging circumstances, we also have a responsibility to support this vital work in any way we can. With industries and citizens depending on plastic, it is isn’t going away any time soon – and there is no silver bullet. Which is why we should all hail the hidden heroes of plastic and give them every opportunity to further their work.
R&D tax credits for packaging, processing and materials handling businesses
Whether you are new to R&D tax credits or you are already claiming them. Allow the expert team at ForrestBrown to evaluate the opportunity in your business and unwrap the full benefit your work deserves.