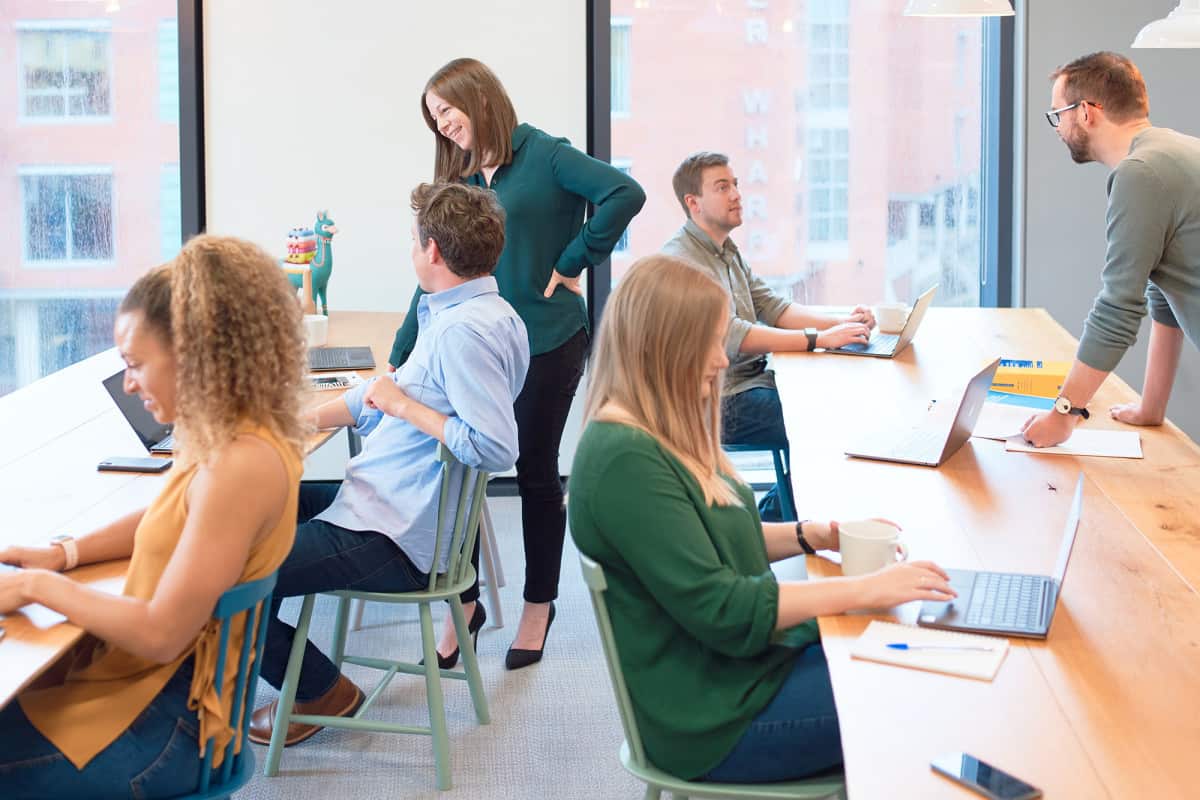
Manufacturing R&D tax advice tailored to your business
Approached correctly, R&D tax relief can transform a manufacturing business. Speak to our team of chartered tax advisers, mechanical engineers and former HMRC inspectors for specialist guidance tailored to you.
R&D in manufacturing
The UK manufacturing industry faces a triple threat: Low productivity, skills shortages and ongoing disruption caused by a changing political landscape. And with ambitious Net Zero targets in place and a ‘Build Back Better’ agenda, now is a critical time for manufacturers.
We know the answer to these challenges: innovation. More and more manufacturing and industrial processes are being automated using modern smart technology. Automation means more productivity, lower costs and, vitally, being less prone to sudden shocks and downturns.
The Fourth Industrial Revolution is well underway. Almost three-quarters of R&D taking place in the UK (69%) is manufacturing innovation. While these investments are essential, they are also capital intensive.
R&D tax relief can make these costs much more manageable – and unlock cash for further investment. At ForrestBrown, we work with manufacturing businesses like yours, to support the ongoing transition to Industry 4.0.
Qualifying R&D in the manufacturing industry
Even as an innovative business, you may be surprised to know the extent of manufacturing projects that can qualify for R&D tax credits.
Qualifying R&D can be found across a diverse range of manufacturing businesses. From pioneering a new anaerobic fermentation method for coffee cherries to curbing unnecessary use of plastic in production to meet green targets, the scope of R&D in manufacturing is vast.
Examples of manufacturing R&D include:
- The development, testing and trialling of new products.
- The digitisation of previously manual machining processes.
- Developing new forms of environmentally-friendly packaging.
- Developing specialised tools to meet high-specification product designs.
- Changing an existing production process to comply with changing regulations.
- Integrating new technologies with legacy back-end systems.
- Making mechanical or digital modifications to production lines to increase productivity.
R&D sub-sectors in the manufacturing industry
Manufacturers we’ve helped
From industry disruptors to established leaders, ForrestBrown has been helping manufacturing businesses get the most out of these powerful incentives for many years.
Read about our work with clients across UK manufacturing:
Colin Jones, Managing Director, Bespoke Handling Equipment
When we met the team at ForrestBrown, we knew right away that they were the right fit for us. It really appealed to us that they didn’t have tie-in contracts and just wanted to do an excellent job.
Alan Ramsay, Finance Director, Dartington Crystal
Although I’m often called by advisers looking to take care of our R&D tax relief claim, I’ve never been tempted to explore their claims. ForrestBrown’s team of tax advisers and sector experts from industry give me the confidence that their advice is in the best interest of Dartington Crystal.
R&D tax relief for manufacturers
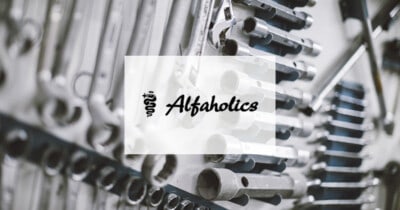
It was thanks to the sector-specific knowledge ForrestBrown has. We can discuss our work in great depth. There is always someone who speaks our language and identifies what we’re doing.
Andrew Banks, Director, Alfaholics
Angela Phillips, Finance Director, CDW Systems
We’ve been working with ForrestBrown for several years now and the funding we’ve received has made a great impact on the business. Not only have we made significant savings on our corporation tax bill, I’m proud to say that we now truly embrace innovation.
A food manufacturer
This dairy products manufacturer introduced a cooling element to their yoghurt fermentation process. The standard method of cooling altered the yoghurt’s flavour, so they designed a new process that cools and ferments the product simultaneously. They received £198,000 for their innovative work.
Stan Bond, Director, Principal Doorsets
I can say with confidence that ForrestBrown are true experts in R&D tax incentives. Their understanding of both the tax rules and our sector makes entrusting them with our claim a no-brainer.
Michael Wiper, Founder & Managing Director, Wiper & True
We spoke with several providers before choosing ForrestBrown. After researching the market, we found their diverse team of experts to be the most credible and professional.
Gary Mason, Engineering Director, NCMT
R&D tax relief helps to demonstrate a financial return for our R&D investment, supporting the case for further focus on innovation. Being able to combine both technical knowledge and expert understanding of R&D tax rules in one team was key.
Assembling the best team for you
ForrestBrown’s team is available for your business on your terms. Whether that means delivering your full manufacturing R&D claim, or offering specialised advice tailored to your specific circumstances, our team of consultants is here to help.
Our manufacturing industry specialists boast unparalleled insight into your R&D, while our chartered tax advisers and accountants oversee your claim and analyse your costs. With HMRC scrutiny at an all-time high, our work is always checked by an in-house quality assurance team – including former HMRC inspectors – to mitigate enquiry risk.
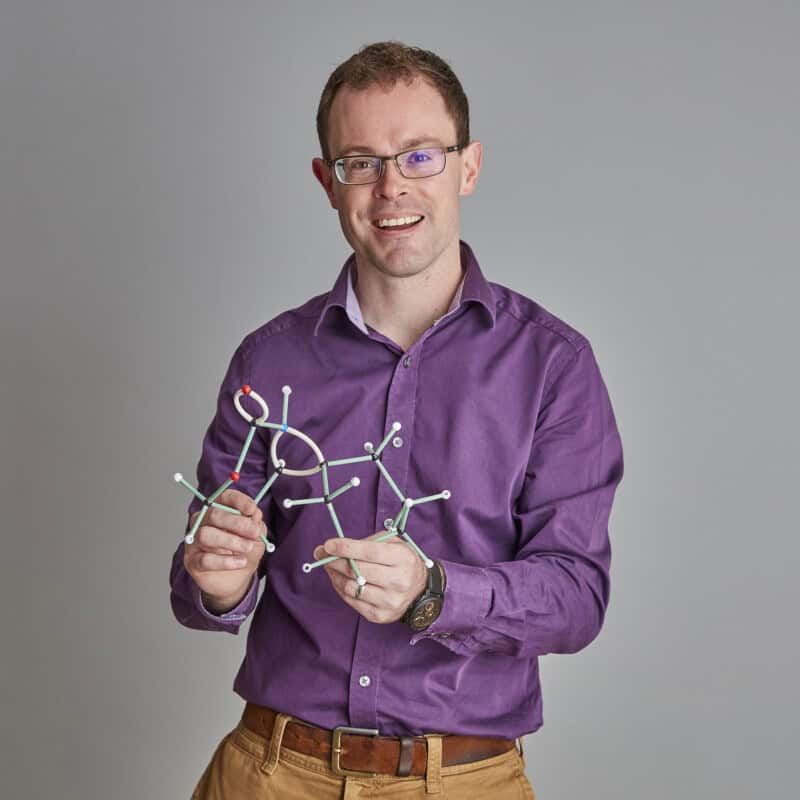
Peter Beavis PhD CSci CChem
Senior Sector Specialist
Peter Beavis PhD CSci CChem
Senior Sector Specialist
- Highly experienced materials scientist.
- Background in food science, pharma and defence.
- Doctorate in organic chemistry.
Expertise & specialisms
- Novel polymers and materials
- Food science
- Defence
- Pharma
Peter’s experience ranges from getting a PhD and MSci in Chemistry and improving confectionery shelf-life to the invention of a patented elastomeric material for improved radiation stability.
His career started with a role as a chocolate scientist at Mars. That was followed by a move to the defence sector, where he finished a nine-year stint as a Senior Materials Scientist at the Atomic Weapons Establishment.
During that period, he authored numerous scientific papers and spoke at international conferences on the synthesis and characterisation of novel polymers and materials. With ForrestBrown, Peter has also been published in The Manufacturer, The Medicine Maker, Interplas Insights, and the Confectionery Production publications.
That scientific and technical capability allows him to quickly understand, challenge and assess clients’ work against the R&D tax credit guidelines. And, it’s seeing the projects companies are able to fund due to the value of their claims – and the excitement they have – that’s driving him.
At ForrestBrown, Peter provides expert peer-to-peer communication for our clients on their technical projects, helping to translate their work into reports for HMRC. Examples of his work include reviewing a claim prepared by a Big Four accountancy firm – and significantly increasing the value of R&D tax relief to their business.
Pete works with our network of associations in the food and drink sector, using his background at Mars as a chocolate scientist to help businesses identify their hidden R&D in this industry. Supporting the activities of our partnerships team, Pete speaks at events, networks with businesses and hosts webinars with industry partners to raise awareness of the value of working with ForrestBrown’s expert multi-disciplinary team to access this valuable incentive.
With an infectious passion for all things science and materials, you can talk to Peter about pharma, food and drink, materials (adhesives, polymers and manufacturing) and engineering sectors.
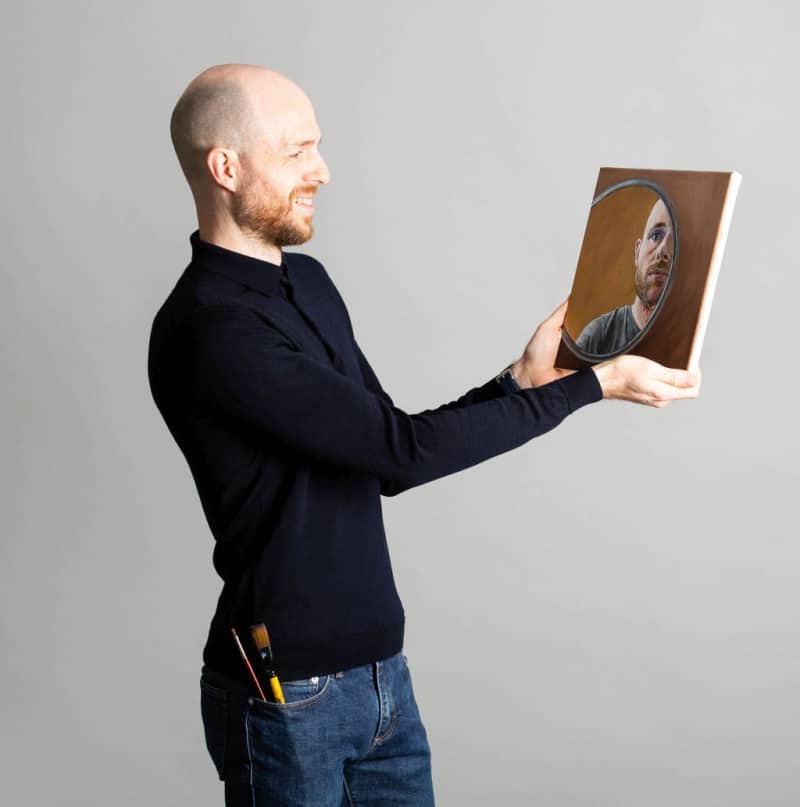
Robin Taylor BEng MIED
Senior Sector Specialist
Robin Taylor BEng MIED
Senior Sector Specialist
- 20 years’ mechanical engineering expertise.
- Specialist in automotive body and electromechanical systems.
- Plays a key role in optimising engineering R&D claims.
Expertise & specialisms
- Mechanical and electromechanical engineering
- Automotive engineering
- Leadership
- Design
Robin is an accomplished mechanical engineer who has worked for some of the world’s most iconic companies. With two decades of industry experience, his knowledge is integral to optimising engineering claims.
After studying Automotive Engineering at the University of Leeds, Robin began his career with a Tier 1 supplier to the automotive industry. He spent five years at this manufacturer developing sealing systems for companies including Toyota, Honda and Aston Martin.
He moved to Bentley Motors and broadened his experience to whole closure systems, including bonnets, doors and tailgates. During this time Robin worked on vehicle projects such as the Mulsanne, Flying Spur, Bentayga and continental GT.
Ten years on, Robin moved to Dyson to work on their electric vehicle project, where he was the engineering manager for closures. As part of this role he managed a large team and had ownership of the body test facility. Several uniquely innovative designs were produced, including several registered for patents.
Robin not only helps our engineering clients, but also works with our wider network of automotive and mechanical engineering industry associations. As a member of the Niche Vehicle Network, Robin draws on his industry experience to support fellow members on the value of their R&D projects; speaking on webinars, joining networking events and participating in sharing insights in industry publications, such as his piece in Automotive Testing Technology International.
Robin brings this wealth of mechanical and electromechanical engineering experience to ForrestBrown. As one of our sector specialists, he helps client companies to articulate precisely where the activities which qualify for R&D tax relief occur. Robins helps to ensure that the technical part of each claim is robust.
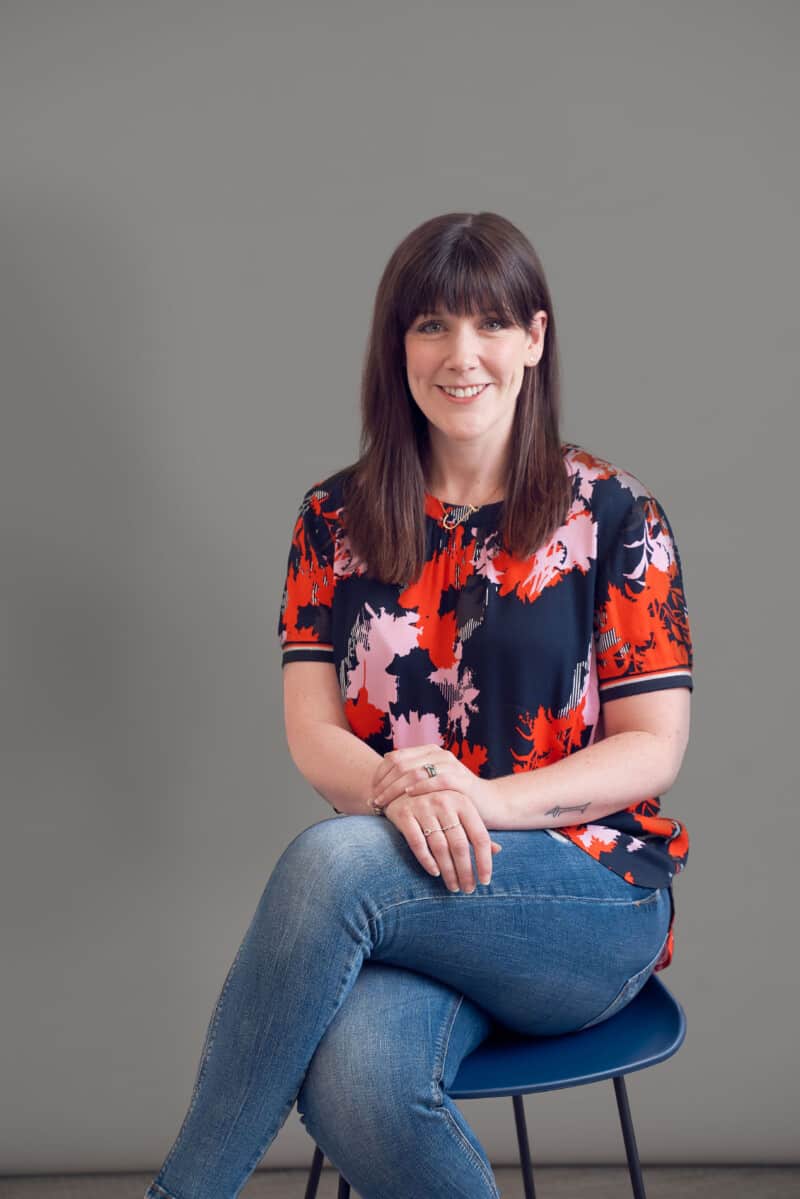
Jenny Tragner CA ATT (Fellow)
Director & Head of Policy
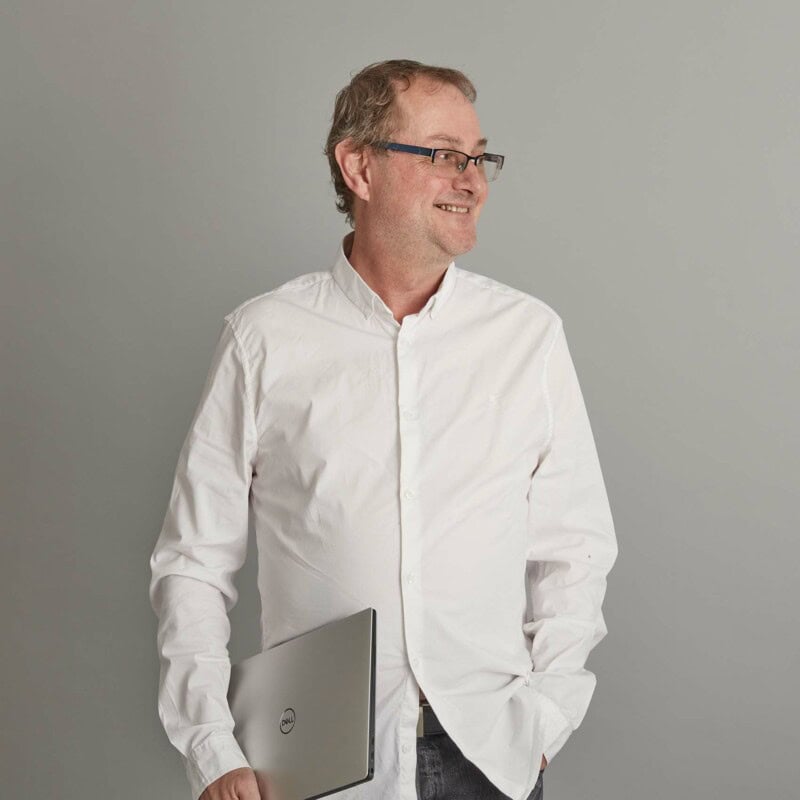
Mark Andrew
Senior Tax Specialist and Former-HMRC Inspector
Mark Andrew
Senior Tax Specialist and Former-HMRC Inspector
- More than four decades of tax experience.
- Provides strategic advice through our advisory and enquiry support services.
- Specialist in R&D tax since 2006.
Expertise & specialisms
- HMRC inspections
- UK taxation
- Training & development
Mark is a former HMRC tax inspector with more than four decades of experience. That includes time working as an inspector in HMRC’s R&D units, providing Mark with indispensable insight on the implementation of the incentive.
Joining HMRC in 1979, Mark went on to specialise in conducting enquiries into companies. He was one of the original tax inspectors assigned to the specialist R&D units in 2006, working in the Croydon unit until 2018.
He joined ForrestBrown in 2019 and his expertise is primarily shared through our enquiry support service, which provides support to clients as well as companies who have prepared claims themselves or through another adviser or partner.
The wealth of experience gained through the combination of public and private sector roles has proved invaluable so far. He helps reassure ForrestBrown’s clients, providing them with a measured viewpoint and advice on their risk profile.
Part of Mark’s drive is the challenge of debating technical issues involving the law. That includes working on Quinn’s landmark tribunal case, which tackled HMRC’s interpretation of the amount of relief available to SMEs for customer-led R&D projects.
In addition to his work in enquiry support, Mark contributes to our in-house development programme, the Learning Lab, which aims to create the next generation of tax professionals.
Find out about a typical day for Mark Andrew in our meet the expert series.
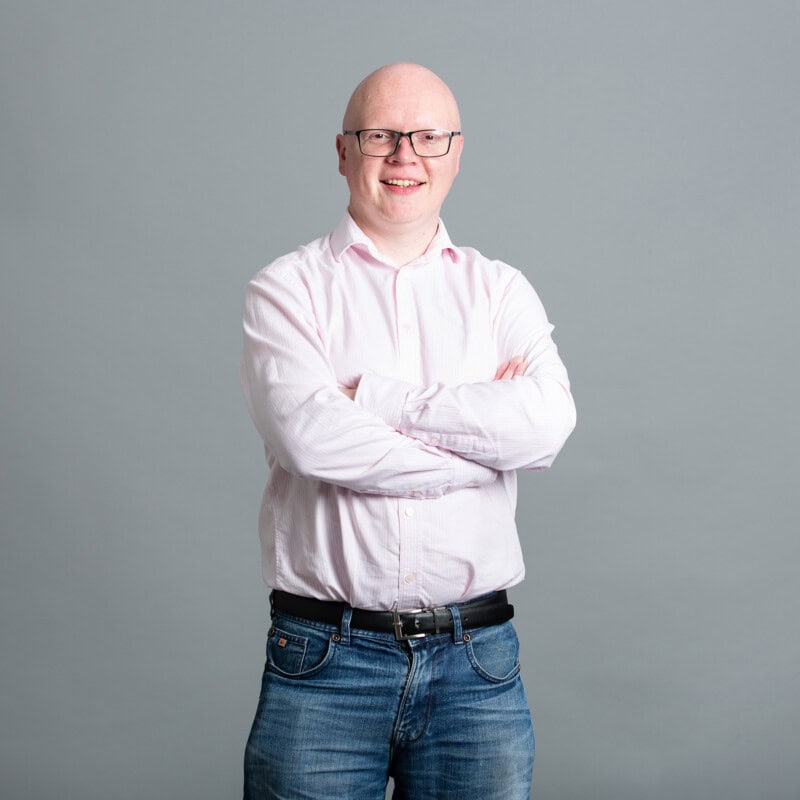
Phil Smith CTA
Technical Lead
Phil Smith CTA
Technical Lead
- Qualified chartered tax adviser (CTA).
- Advised hundreds of businesses on R&D tax relief.
- Provides a range of specialist R&D tax advice.
Expertise & specialisms
- UK taxation
- Breaking down complex concepts
- Manufacturing
- Engineering
With a growing interest in innovation, Phil joined ForrestBrown in 2014 to work with our manufacturing and engineering clients. He trained at Cooper Parry in Nottingham and qualified as a chartered tax adviser in 2009. Phil then moved to Burton Sweet and later Hazlewoods, where he advised owner-managed businesses on personal and corporate taxation. He brings over a decade of experience to our team.
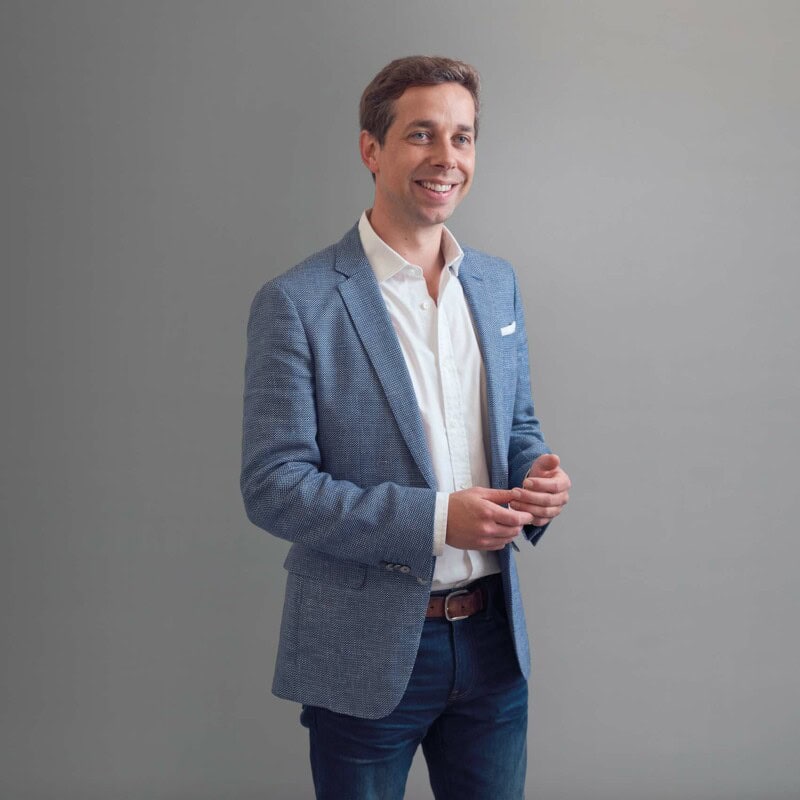
James Dudbridge LLB
Director
James Dudbridge LLB
Director
- Leads our tax advisory practice, FB Consulting.
- Solicitor specialising in corporate and personal tax.
- Track record of success at first-tier tribunal tax chamber.
Expertise & specialisms
- Complex corporate structures, including international groups
- HMRC disputes including compliance checks and appeals
- UK tax law
James leads our tax advisory practice, FB Consulting, providing award-winning R&D tax relief expertise to businesses and accountants. This can include modelling and forecasting, risk profiling and benchmarking, and advice on compliance and methodology for large corporates.
With a legal background and extensive experience dealing with HMRC, James brings incisive insights to tax disputes, developing strategies to achieve the best possible outcome for clients. For example, he successfully led ForrestBrown’s support for Quinn (London) Limited in a 2021 landmark tribunal case challenging the interpretation of subsidised R&D expenditure.
James and the FB Consulting team provide specialist advice, working alongside a company’s general advisers, including due diligence relating to R&D tax relief pre and post transactions and R&D in complex, international groups.
A solicitor who specialises in tax advice for corporates and individuals, with a focus on cross-border and international issues, James trained and qualified at a top London law firm before relocating to Geneva to help set up the firm’s Swiss office. On returning to the UK James worked in the tax team of a leading Bristol and London-based law firm, before joining ForrestBrown in 2019.
James has contributed commentary on R&D tax relief and tax disputes to publications including Bloomberg Law and International Tax Review.
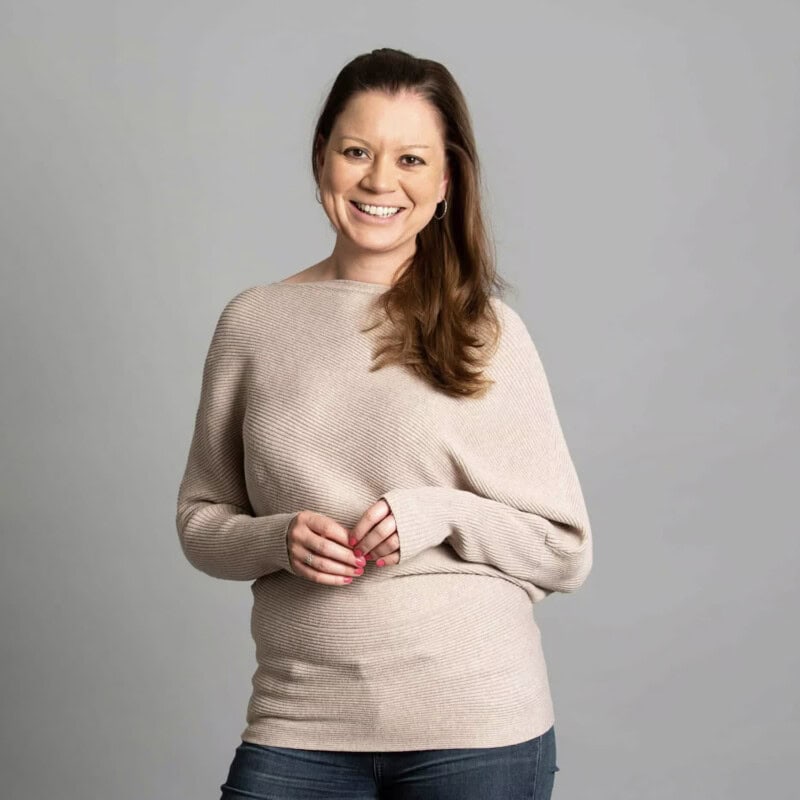
Jayne Stokes ACA
Associate Director
Jayne Stokes ACA
Associate Director
- ACA qualified.
- Former director at a Big Four firm.
- Advises innovative businesses on R&D tax relief and tax disputes.
Expertise & specialisms
- HMRC enquiries and tax disputes
- Accounting
- Chemistry
Jayne is an experienced chartered accountant with Big Four experience, who has worked in both the UK and Middle East. She is a senior adviser in FB Consulting, ForrestBrown’s specialist tax advisory service.
Jayne joined ForrestBrown in 2020 and brings a wealth of experience in leading complex tax advisory projects, which helps her provide invaluable advice to our clients. She also plays a key role in assessing and managing tax risks and leading client relationships with HMRC.
Drawing on her science background, she takes particular interest in the pharmaceutical and medical sectors. In her role with ForrestBrown, Jayne is focused on developing our advisory services to help more businesses across the UK benefit from R&D tax relief. This includes working with clients and accountants to create robust claims and providing strategic advice or specialist support should HMRC open an enquiry.
After completing a Master’s degree in Chemistry from the University of Sheffield, Jayne began her career with Deloitte in 2006. She was based in the entrepreneurial business tax practice and studied for her ACA qualification.
In 2010, she moved to Dubai to help establish Deloitte’s international tax practice for the Middle East region. She managed a diverse portfolio of clients including large multinationals, owner-managed companies and startups.
Why choose ForrestBrown
What does the best R&D tax advice for your manufacturing business look like? The answer is unique to you. ForrestBrown will customise our service to match your requirements. Whether that’s handling your entire claim, or supporting you with specific expertise on a consultancy basis.
R&D, especially in the manufacturing industry, encompasses a wide array of different work. Don’t cram your diverse innovation into a rigid R&D tax service. ForrestBrown’s flexible approach helps you make claims that are robust, cost-effective and timely.
- Telephone
- 0117 926 9022
- hello@forrestbrown.co.uk
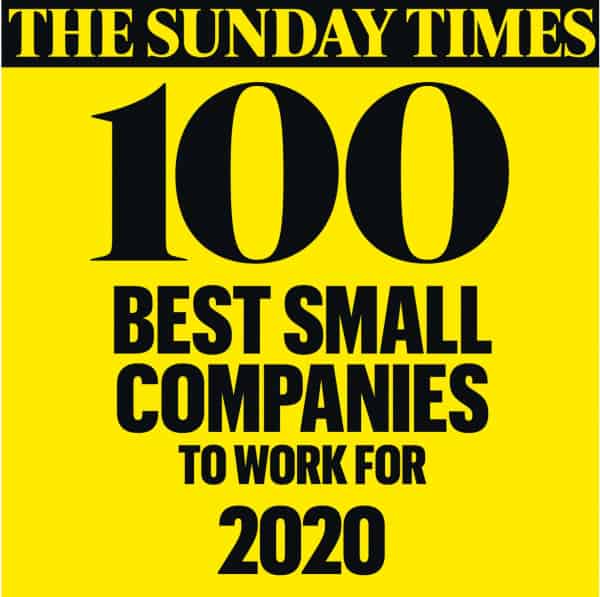
#73 out of 100
The Sunday Times Best Companies to Work For
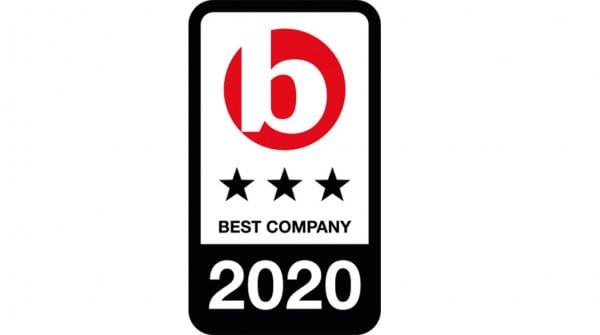
3 star accredited
Best companies – “extraordinary” levels of employee engagement
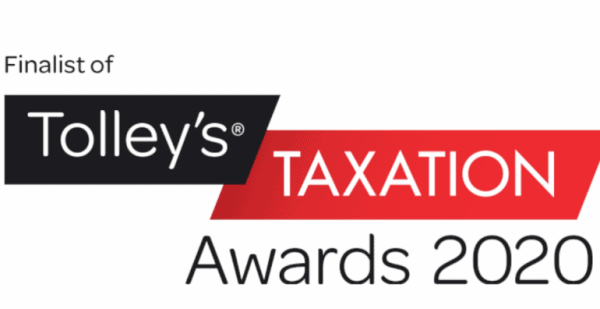
Finalist
Best Employer in Tax

Finalist
The ECI B2B Business of the Year
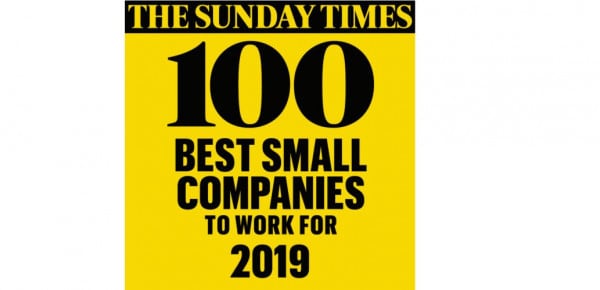
#77 of 100
The Sunday Times best small companies to work for
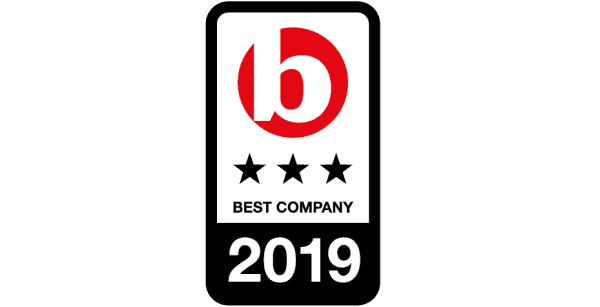
3 star accredited
Best Companies – “extraordinary” levels of employee engagement
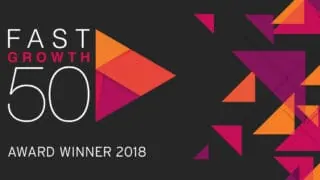
#1 of 50 & category winner
Overall winner & financial & professional services winner

3 star accredited
Best Companies – “extraordinary” levels of employee engagement
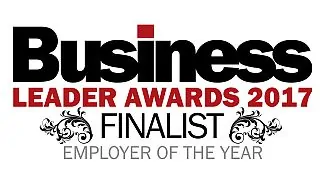
Finalist
Employer of the year
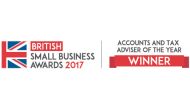
Winner
Accountants and tax adviser of the year
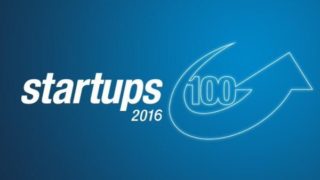
Ranked
#13 of #100
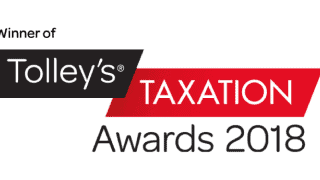
Winner
Best independent consultancy firm